Inspiring the reuse and recycling of building materials
The construction industry, and the materials it uses, are responsible for more than a third of global resource consumption. This has significant repercussions on carbon emissions and ecosystem degradation. Reusing and recycling construction materials is an effective way to reduce the resource use and carbon intensity of the built environment.
It was once common to reuse materials in new buildings – but it’s now the exception, not the rule. When reused or recycled materials are used, it’s usually at a superficial level that doesn’t approach the scale necessary to have meaningful climate impacts.
There are many reasons reused materials aren’t more widely used. One is the mismatch between supply and demand of reusable and recyclable materials. This means upcoming projects cannot rely on availability of reused or recycled material – which can disrupt timelines. A limited or inconsistent supply means there is no demand for materials at scale.
Another reason is a lack of trust in the quality and reliability of reusable and recyclable materials compared to new. This perception limits their applications and potential for use, with insurance providers often declining to underwrite reused materials. There are real but manageable challenges to overcome around limits in structural applications and potential contamination by hazardous materials.
There’s also a lack of standard practice on how to identify and report materials suitable for reuse and recycling. Many contractors are unaware of, or unable to implement, the demolition processes that document and preserve building materials.
A better system is possible
In the face of these challenges, it can be difficult to highlight the potential environmental and economic benefits of using reused and recycled materials. Without consistent and standardised reporting, measuring cost and carbon footprint benefits is a costly exercise in itself.
Improving this system is possible. Urban mining means recovering and reusing cities’ building materials – high-quality reusable and recyclable materials can be extracted from existing buildings if the right demolition techniques are used. This can play a key role in helping built environment stakeholders reduce their environmental impact, costs and waste.
A secondary material reuse market can be created by applying standardised documentation, using digital and physical infrastructure, establishing behaviour change mechanisms and sharing case studies highlighting benefits – as well as supporting city-wide policies.
This chapter looks at practical steps to achieve these goals. It reviews CIRCuIT’s findings on pre-demolition audits supporting city-level policies, shares practical demonstrators and business cases that can be taken from them.
Urban mining in action – examples of material reuse and recycling
Working with each other and local built environment stakeholders, partner organisations in the four CIRCuIT cities developed and evaluated 12 demonstrator projects to showcase urban mining strategies and the benefits they can deliver. Four are showcased here.
Below is an overview of each project, the techniques used and key learnings.
Full overviews including detailed carbon and cost assessments of all demonstrators can be found at circuit-project.eu/post/latest-circuitreports-and-publicationsCopenhagen
Gladsaxe school / The Swan - Selective disassembly
Physical Demonstrator
Overview
The Gladsaxe school is an interesting case for PDA assessment because it represented two types of buildings – it was built in 1937 and extended in 1967.
Materials from the school were used to construct a new kindergarten on the same site, making it easier to plan for urban mining (see page 2-10). This included wood recovered from demolition in the kindergarten’s entry hall, wooden trusses, steel sheets, pantiles, masonry and specific fixtures and accessories such as lamps and sinks.
Reuse of the wooden trusses was the main focus of the project, with six forming the load-bearing roofing elements in the new kindergarten’s entrance hall.
Nearly 6,000 tonnes of concrete were also crushed and used for the kindergarten’s foundations and site backfilling.
Key actions taken
The pre-demolition audit involved an interdisciplinary team, with stakeholders from the entire construction value chain. Timber rafters from the roof were carefully cut free according to predefined and agreed cutting lines. Three types of steel cladding were dismantled from the building and bricks were taken down using a Cat digger and cleaned manually from mortar. Roofing tiles were also selectively dismantled from the school.
Key findings
The pre-demolition audit of a building should be a process that involves stakeholders from the entire construction value chain to ensure the highest possible level of recycling and reuse. In particular, the demolisher of the existing building and the architect/developer of the new building should go through the existing building together to discuss and agree on reusable/recyclable items.
It’s crucial to use expert reuse consultants for the initial building mapping who can steer cross-disciplinary processes so circular practices are used rather than linear approaches. An open house at the demolition site, a virtual open house or a digital model, could be used early on to connect built environment stakeholders with each other. They can then explore how they would work together to reuse or recycle materials from the existing building.
Storage of extracted materials should be a consideration. For example, the timber extracted from the Gladsaxe school needed to be stored in a place where it was covered and ventilated, so it didn’t rot.
If a developer includes the reuse of building materials in their tender, it will be calculated in project finances from the beginning. That means it’s less likely to be overruled later in a project due to economic or practical reasons.
If building materials are initially regarded as reusable products rather than waste, regulations may state they don’t have to be checked for hazardous substances. As a result, it’s important that an initial screening for hazardous substances takes place along with the PDA to ensure materials that could harm the environment or people don’t remain in the built environment.
Reusing timber is an opportunity to extend the carbon storage of wood. Growing trees store carbon, which is then released when wood is burned. However, assessing wood for reuse is relatively simple, if standards are followed. Reusable wood may be deformed or crooked, which should be considered when designing a new building.
Die Musterbude – Testing the performance of recycled concrete mixtures
Physical Demonstrator
Overview
Die Musterbude is an innovative project that involves the construction of a small cabin using seven types of recycled concrete. Recycled concrete has been used for decades – but this project tested new mixes featuring materials like recycled sand and waste materials from demolished buildings against conventional concrete. The project aimed to assess the technical and environmental qualities of the recycled concrete mixtures against a standard concrete mixture that uses new aggregates.
The recycled concrete, which is derived from crushing and reusing excess concrete from demolished structures, is the primary construction material for the Musterbude.
The project allows a deeper understanding of how recycled concrete performs in real-world applications and its potential benefits in terms of sustainability and material circularity.
By demonstrating the successful use of recycled concrete aggregates, the project sets a compelling case for sustainable construction practices that advance the circular economy in construction.
Key actions taken
The project produced various aggregates from construction and demolition waste. They were tested for optimal screening and washing both in the lab and in the finished construction. Out of this process, seven new recycled concrete recipes were developed. Life cycle assessment and costing was carried out.
Key findings
The project team found mixtures with a higher percentage of recycled concrete have a lower environmental impact. However, mixtures with a higher percentage of recycled concrete lead to more water consumption because of the porosity of recycled aggregate. The amount of water could be reduced by using polycarboxylate superplasticizers (PCEs) in the concrete mix (a chemical admixture) and pre-washing aggregates.
The Hamburger Mische mixture, which contains 100% mixed construction and demolition waste, achieved good concrete strength and surpassed expectations.
Because of these positive results, the mix will be further improved and used locally in Hamburg.
Tikkurila school warehouse – Reusing red clay bricks
Physical Demonstrator
Overview
Reclaimed red clay bricks, including from the National Theatre of Finland, were reused to construct a small storage building in the yard of the Tikkurila Pavilion School. Bricks were identified as a prevalent and reusable building material in the pre-demolition audits of two demolition cases in Vantaa.
The aim of the demonstrator project was to develop cost-effective methods to investigate the quality of deconstructed bricks (and potentially other materials). It was also to assess the environmental and economic performance of reused bricks against virgin bricks.
Key actions taken
Bricks were deconstructed with hand-held power tools and an excavator. An assessment was carried out between material properties acquired with indirect (non-destructive) methods and those acquired with direct (destructive) methods. There was also an assessment of the environmental and economic performance of reused bricks in comparison to virgin bricks. Recommendations were noted about appropriate methods and sample sizes. Ultimately, reclaimed bricks were used to build the storage building.
Key findings
Indirect methods to study the material properties of reclaimed bricks include assessing the colour of a brick and its pitch when struck to sort into different categories. Compression strength and freeze-thaw durability of a reclaimed brick can be evaluated with ultrasonic pulse velocity. Both are rapid, low-expense tests that can be performed at a demolition site. This contributes to the cost-effectiveness of the reuse process. However, only laboratory tests can determine compression strength and freeze-thaw resistance accurately.
Reused bricks must be selected carefully for the right area of a building to ensure an ‘attractive’ side of the brick is visible. This selection takes more time than using new bricks.
Glulam from secondary timber
Physical Demonstrator
Overview
The London demonstrator investigated the technical and logistical feasibility of upcycling reclaimed timber into new building components.
This involved retrieving timber from demolition sites, characterising and quality-testing the material, preparing it for manufacture and fabricating new glued-laminated timber building components.
Key actions taken
Timber was reclaimed from building demolition sites. The reclaimed timber was characterised, visually and mechanically, to prepare it for the manufacturer. New laminated timber building components were manufactured from reclaimed timber.
Bending tests and shear tests were carried out on the glulam beams. Test results were compared with benchmark results of glulam fabricated from virgin timber. Finally, recommendations were provided on deconstruction, regrading and manufacture in relation to secondary timber laminated building components.
Key findings
There was good correlation between non-destructive and destructive testing of the stiffness of manufactured secondary timber glulam beams. As stiffness is a good indicator of strength, this suggests that secondary timber glulam beams could be commercially tested using non-destructive methods (as is the case with virgin glulam products) to verify product performance.
The glulam beams made of secondary timbers performed to structural glulam standards.
No additional time is needed for removal of timber compared to business-as-usual demolition practices. If it takes no longer to remove the timber then there isn’t a cost premium on accessing the material.
Identification and removal of screws, nails and staples is crucial to avoid damaging the tools used in the glulam manufacturing process.
Longer secondary timber lengths, ideally 1.5m or longer, enable a cost-effective manufacturing process by minimising the number of finger joints required.
Optimising the pre‑demolition audit
Pre-demolition audits (PDAs) are critical to driving recycling and reuse in construction.
Why PDAs?
A PDA is a comprehensive and systematic assessment of the quantity and quality of elements and materials left after a building’s demolition. It can be used as a tool to identify potentially reusable and recyclable components. When completed well ahead of demolition this information can be fed into a digital platform where professionals can see what materials will become available for upcoming designs.
Implementing PDAs in policy
Currently, PDAs are not required as part of the demolition process in most cities.
Where they are required or encouraged, they are often not compulsory, standardised or set up to support circularity. Existing policies and demolition auditing methodologies also typically focus on hazardous materials and their waste codes. This frames outgoing materials as waste rather than usable resources. Even when detailed information is collected, it’s not standardised. This doesn’t allow for the aggregation necessary to share material information at scale. Making sure planning policy requires PDAs in a standardised format would overcome these challenges.
Recommendations to successfully embed PDAs in city policy
Establish digital system to capture PDA data
Ensure city planning data systems can capture the material data included in PDAs. This will allow the collected data to be used to support secondary material reuse.
Standardise PDA format and guidelines
Align PDA reporting with local best practice, in discussion with industry, to ensure data can be transferable.
Make PDAs mandatory
Once a digital system can actively use and support PDA submissions, the PDA should be made mandatory. Efforts should be made to give the PDA a legal basis and make it part of a corresponding law. The current voluntary nature of the PDA does not create incentives for increased use. Due to the country-specific legislation in the construction sector there isn’t an EU-wide consistent way of integrating the PDA into legislation. Accordingly, it cannot be recommended to make the PDA mandatory on a European level. Instead, it is recommended to make the PDA mandatory at the national or local level.
Expand PDAs to include pre-redevelopment audits
To fully capture all the potential material flows in the city, PDAs should also be carried out for retrofit or renovation projects.
Frame PDAs as part of the building life cycle
Rather than viewing the PDA as a standalone procedure dealing with ‘waste’ it is recommended to integrate it into the building life cycle. It is recommended to perform the PDA as early as possible and to frame the identified materials as resources. Doing this will enable long-term planning processes and more transparency in intended handling of building stock.
Make PDAs more understandable and intuitive
The title ‘Pre-demolition audit’ can be unnecessarily confusing for some people. Changing it to something like ‘Urban mining audit’ or ‘Circular material audit’ could help spread awareness.
Update PDA tools
The tools used to complete the audits should also be updated to be more intuitive and user-friendly than the current Excel models.
Make PDA information accessible to all stakeholders
To capitalize on all the benefits of completing PDAs, the data must be accessible to the industry at large: collectively they provide a database of building components that will soon become available.
Incorporate the PDA steps into contracting
For public tenders: Perform the first step of the PDA: element and material assessment before issuing the tender and use it to make a detailed performance description. The demolition contractor will then respond with the second step of the PDA: management options as part of the offer. The contract will make the procedure legally binding.
How cities are embedding pre‑demolition audits
Though not formally required, the CIRCuIT project cities have already implemented PDAs in some policies to varying degrees. The range of approaches illustrates the various ways cities can embed PDAs into current practices.
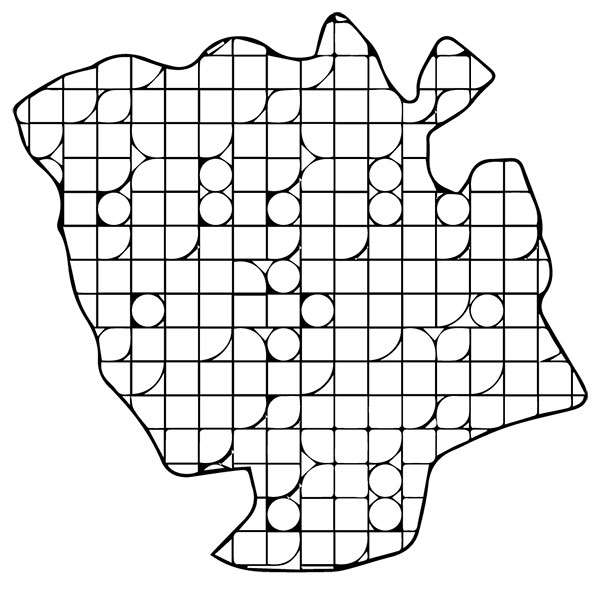
Copenhagen
For most projects, hazardous waste screening is already mandatory in Denmark, while PDAs mapping material quantities and quality is voluntary. The city has made PDAs mandatory for their own projects. Work is being done to create a national standard for both environmental mapping and PDAs. This includes standardising reporting and a basic training programme that is required so that only trained auditors can have their work approved. In the meantime, the municipality is working on creating a standard procedure for PDAs in owned buildings in which a digital platform can handle all the steps and gather data in one place.
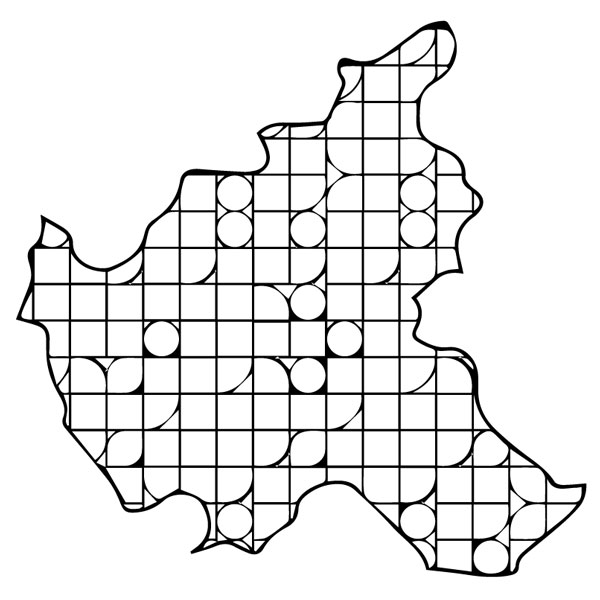
Hamburg
PDAs are not yet required or recommended in Hamburg, but there are requirements for hazardous waste screening and separation. Demolitions are often completed on short notice. This means there’s limited time to realise the benefits of PDAs. The City of Hamburg is examining if they can make a digital PDA available as an open data source through the city’s website for construction projects. At the same time, future integration of PDAs in public tenders is being discussed.
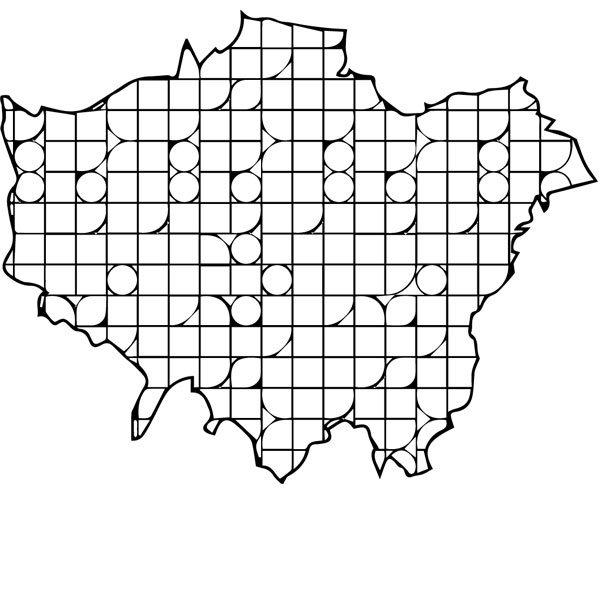
London
PDAs are not the norm in London. However, in recent years there has been an increase in their use on larger developments. Most PDAs are completed to earn Building Research Establishment Environmental Assessment Method (BREEAM) credit or to fulfil Circular Economy Statement (CES) requirements. These were introduced in 2020 and came into effect in 2021. Policy on PDAs will most likely continue to be addressed through the CES policy at city and borough level.
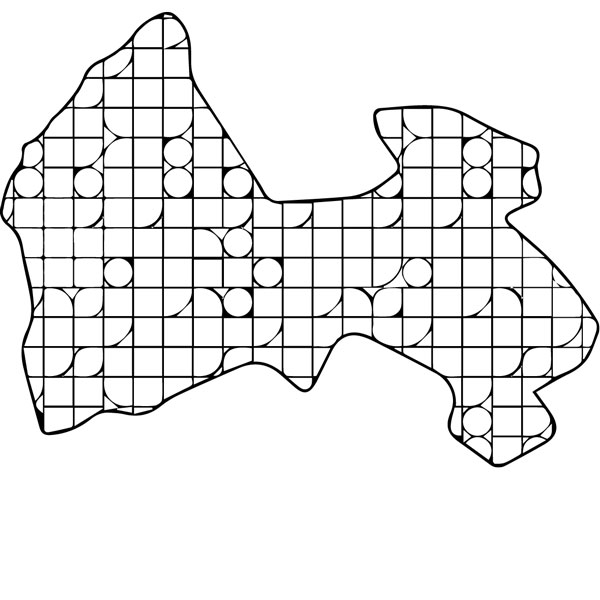
Vantaa
PDAs are currently conducted in all demolition projects owned by the city of Vantaa. To support developing demolition data collection in the current registers of the city, Vantaa has joined the national Green Deal on sustainable demolition, which requires systematic use of PDAs. The Green Deal is with the Ministry of the Environment and sustainable demolition agreements are valid until 2025. PDAs are currently voluntary in Finland. The new and reformed Building Act will come into effect at the beginning of 2025. It will oblige a waste and demolition material estimate before a demolition permit can be granted, and a waste and material statement after the demolition has been finalised.
Developing an optimised pre‑demolition audit
The CIRCuIT project developed an easy-to-understand methodology, template and checklist to support built environment stakeholders to carry out PDAs and increase material circularity in their local area.
These outputs were tested in 12 demolition demonstrator projects: three each in Copenhagen, Hamburg and London (Please see page 2-4 for more information).
Pre-demolition audit methodology
Follow these steps when using the PDA template and checklist developed by CIRCuIT partners.
Step 1 – Desk study
Analyse relevant documents to collect information about the building’s history. The age of building and/or past works are essential information and related to the presence of hazardous materials such as asbestos or heavy metal-contaminated materials. Carry out initial inventory of materials.
Step 2 – Field survey
The auditor should visually inspect all parts of the site to be demolished. This phase is important to verify quantities of materials, evaluate their condition and potential for reuse, and estimate the amount of waste from demolition. Inventory of materials is completed with the field survey.
Step 3 – Inventory completion
The inventory happens during the desk study and field survey. It includes the type and quantification of reusable and recyclable materials and components, as well as hazardous materials and eventual waste fractions. Record through photos, comments or advanced scanning approaches that allow a faster execution of the audit and easier interpretation.
Step 4 – Recommendations
The audit provides recommendations on how to:
preserve valuable components and materials during the demolition activities
safely remove hazardous and/or waste fractions
manage waste logistics and operations.
Step 5 – Report
The report must include information on the project, the information collected during the desk study and field survey, and any information that can be useful for the owner, contractor or any other stakeholder involved.
Pre-demolition audit template
The optimised PDA template developed as part of the CIRCuIT project is available to download at circuit-project.eu/post/latest-circuit-reportsand-publications
Recommendations to increase reuse and recycling of building materials
Digitize planning process and allow open access to data
Improved material data transparency and material information improves market confidence, reduces risk and provides opportunities for long-term planning. Improved material information should facilitate improved quality assurance and consumer material choice to compete with virgin construction materials and enable more opportunities for closed loop reuse and recycling of materials.
Relevant stakeholder(s) Public stakeholder(s)
Establish materials exchange platforms for city and/or region
Material exchange platforms provide the data infrastructure necessary to facilitate material exchanges showing the material supply and demand.
Relevant stakeholder(s) Building industry
Connect data collected during planning with material exchange platforms
To take advantage of the high-quality data collected during the planning process, connect this data with material exchange platforms where possible. This will allow information coming from planning requirements, such as the PDAs, to be used practically on existing networks without delay.
Relevant stakeholder(s) Public stakeholder(s)
Develop alternative quality assurance methods
Develop alternative non-destructive methods for quality assurance of reused materials
Relevant stakeholder(s) Building industry
Develop alternative funding options for pilot projects
Provide alternative funding schemes for ambitious circular projects in public building projects to meet increased up-front costs related to innovative secondary material use.aterial use.
Relevant stakeholder(s) Public stakeholder(s)
Temporary urban storage facilities
Establish temporary storage facilities for reuse materials from private or public demolishing sites.
Relevant stakeholder(s) Building industry Private stakeholder(s) Public stakeholder(s)
Standardised secondary materials
Pursue and develop standardised secondary building materials and components for large-scale market uptake.
Relevant stakeholder(s) Building industry Public stakeholder(s)
Establish training on improved selective demolition
There is room for improvement in selective demolition technologies and workforce skills. Lack of industry knowledge and/or experience on damage-free disassembly leads to degradation of materials which severely reduces circular opportunities. Skilled and experienced contractors to guide circular processes are crucial.
Relevant stakeholder(s) Building industry Public stakeholder(s)
Promote and educate on material reuse and recycling
Addressing lack of knowledge about the value and benefits of material reuse and recycling requires awareness and educational initiatives. Industry associations, government agencies and construction companies can collaborate to raise awareness about the environmental advantages, cost savings and sustainability benefits. This can be achieved through workshops, seminars, training programmes and information campaigns highlighting successful case studies and showcasing the positive impact of material reuse and recycling.
Relevant stakeholder(s) Building industry Public stakeholder(s)
Develop alternative disassembly practices
Time-consuming manual handling is often required for the high precision tasks of removal and cleaning building elements and components. Innovative technology and equipment is needed to reduce labour-intensive practices.
Relevant stakeholder(s) Building industry
Making the case for reusable and recyclable building materials
A ‘business case’ makes the case for change. It is directed at a specific audience who can make the proposed change and describes actions to be taken outside of BAU and expected outcomes. Four of the business cases that were developed drawing on the carbon and cost analysis of the CIRCuIT urban mining demonstrators projects, are shared here.
Each business case includes five perspectives presented under the headings: strategic, financial, feasibility, risk and scalability. Together these commentaries and the demonstrator templates provide evidence on the benefit of investment in the proposed changes for both the decision maker and the community.
A full list of all business cases developed from demonstrator results can be found in Appendix A1.2
A. Public and private asset owners can assess cost and carbon saving opportunities from reuse across projects and asset portfolio by commissioning and acting on pre‑demolition audits.
Strategic: Public and private asset owners can identify opportunities to make cost and carbon savings through reuse of materials across projects and assets in their portfolio. They can achieve this by commissioning PDAs in the early design stages of major redevelopment and building upgrades.
Financial: The cost of commissioning a PDA is small in the context of construction costs. One demonstrator found a 12% saving in construction costs through on-site use of recycled aggregates. A demonstrator comparing deconstruction and component resale to demolition and scrap value of a structural steel frame found that the cost premium involved in deconstruction is £50/tonne and additional resale value is £80/tonne. However, if it is assumed that 20% of the deconstructed steel is lost to cutting, the deconstruction option becomes 8% more expensive than BAU. A demonstrator reusing timber trusses on site also reported increased costs, largely due to additional handling, processing and fitting costs compared to BAU. A demonstrator comparing reclamation of bricks laid in cement mortar using hand-held power tools and an excavator found that using hand-held tools produced reusable bricks at a higher cost than other reclaimed bricks on the market. However, using an excavator produced reusable bricks that were cheaper than other reclaimed bricks (by 48%) and cheaper than virgin bricks (by 24%).
Feasibility: There is increasing familiarity with PDAs in industry and capacity for carrying them out in early design stages, in line with CIRCuIT recommendations. However, many secondary material supply chains remain in their infancy and do not have the economies of scale enjoyed by conventional supply chains.
Risk: CIRCuIT policy recommendations include making PDAs mandatory for all projects or all government projects. Building this into procedures now, demonstrates leadership from local authorities and enables forward-thinking developers to stay ahead of legislation.
Scalability: The potential impact of PDAs increases as more are carried out. With more reusable materials identified and made available through digital platforms, data collection will reach a tipping point where it becomes a fertile place for specifiers and procurers to source materials they need. That scale will reduce the costs of deconstruction, processing and testing. Across a portfolio, there may be timely opportunities to direct components from one project to another. Local authorities can also offer materials at low cost to projects that achieve other goals such as social value. In the medium term, aggregated findings from PDAs provide data that can be used to support future policymaking. Innovative surveying methods could improve the quality of information generated and/or reduce the cost of PDAs.
Related demonstrators: Demonstrator 2 – Offakamp, Demonstrator 4 – Gladsaxe School / The Swan, Demonstrator 6 – Hyltebjerg skole, Demonstrator 7 – Hevoshaka school, Demonstrator 8 – Vantaankoski school, Demonstrator 10 – Component reuse of retail unit, Demonstrator 11 – Leadenhall
G. Local authorities can help to create circular supply chains by driving demand for novel remanufactured secondary materials and adopting their use in public projects.
Strategic: Local authorities can reduce embodied carbon emissions in line with their own carbon reduction objectives by taking a leading role in briefing design teams to specify secondary materials. This will also help break down barriers to wider adoption of novel materials.
Financial: New remanufacturing initiatives may not be able to deliver like-for-like materials cost neutrally when compared to existing manufacturers that operate with significant economies of scale. In the demonstrator project on which this case is based, the time involved in deconstructing timber framing was estimated in general to add 15% to the demolition contractors’ costs. This would lead to more expensive feedstock for glulam production than using primary timber as usual. However, there is a holistic economic benefit to the area if more construction spend is retained in the local economy. This spend also helps new businesses expand and reduces their costs, increasing the competitiveness of circular supply chains in the longer term.
Feasibility: Adopting novel materials requires strong impetus from those commissioning construction to set a ‘direction of travel’. Officers in development and regeneration roles will need to understand the reasons for the policy and act as custodians as it is enacted in briefs and challenged through the course of a project’s development. Appointed design teams will be asked to specify materials in a way that differs from their normal practice. Likewise, contractors will be asked to build with materials that may vary from those they are familiar with. Clarity of rationale and awareness of carbon and circularity will be key to resisting pressure to revert to BAU.
Risk: Association with innovative, circular businesses can enhance the reputation of a local authority among staff, residents and industry. The opportunity cost of achieving carbon savings or other environmental benefits should be weighed against other options for achieving the same benefits. The starting point is to understand the scale of benefits. In the demonstrator case, using secondary timber in glulam manufacture was found to achieve a 40% reduction in embodied carbon (cradle-to-gate), and almost a 200% increase in the biogenic carbon stored in wood (grave-to-cradle-to-gate).
Scalability: The ability to scale this business case depends on availability of novel secondary materials ready to be supplied to major projects. The emergence of these supply chains can be supported by developing physical and digital infrastructure that creates a more effective market for secondary materials. It should also make available materials more visible and reachable by remanufacturing businesses. Organisational infrastructure will develop workforce skills and capacities for deconstruction, testing and recertification and form links in supply chains. Greater demand for secondary materials from across the market, driven by progressive purchasing, tighter regulation of whole life carbon or carbon pricing will create more opportunities for new circular businesses.
Related demonstrators: Demonstrator 12 – Glulam from secondary timber
P. Local authorities can help to create supply chains for secondary materials by establishing circular economy construction hubs closer to city centres.
Strategic: Local authorities can reduce embodied carbon emissions of their own buildings, and other developments under their jurisdiction, by allocating sites for circular economy construction hubs and facilitating partnerships to establish and manage them.
Financial: Circular economy construction hubs improve the likelihood of retaining value from materials in the local economy. This can reduce the length of supply chains, minimising exporting waste and importing materials, and increasing local employment. Reuse opportunities are sometimes missed due to lack of available space to store materials or inflated costs because materials need to be taken to remote storage.
Investigating potentially reusable materials was found to be a time-consuming exercise that requires significant effort from the design team. In one demonstrator this accounted for around 10% of the total cost involved with reusing glulam beams (although total costs were 12% less than new glulam). As the reuse process becomes more visible in cities through hubs, and more familiar to teams, the transaction costs involved with new ways of sourcing materials will come down.
Feasibility: Leveraging existing skills, capacity and experience through partnerships with organisations already involved in managing related sites will be key to establishing them. This could include demolition contractors, reclamation yards, builders’ merchants, construction consolidation logistics centres, developers, universities and colleges and production facilities.
Risk: Temporarily using disused brownfield sites earmarked for long-term redevelopment may provide opportunities to road-test circular economy construction hubs. This can activate sites that are otherwise providing no social value and detracting from the urban environment.
Scalability: This case can be seen as a step in evolving urban waste management infrastructure to circular economy infrastructure. Policy targets for net waste self-sufficiency (e.g. the London Plan policy of the equivalent of 100% of London’s waste being managed within the city by 2026) should be established to support development of such sites. In the demonstrator projects on which this case is based, local recirculation of materials achieved carbon emissions reductions of 2-6%, 8%, 40% and 47%.
Related demonstrators: Demonstrator 1 – Luruper Hauptstraße, Demonstrator 3 – Musterbude, Demonstrator 5 – Stablen / The Stack, Demonstrator 12 – Glulam from secondary timber.
U. Demolition contractors can achieve new revenue streams by becoming retailers of recovered materials.
Strategic: Demolition contractors can rebrand as urban mining specialists and open up new revenue streams by recovering more materials and finding markets for their reuse, remanufacturing or high-quality recycling.
Financial: Demolition contractors already seek to minimise disposal costs by identifying materials that can be sold by reclamation yards. But this is usually limited to high-value goods for heritage projects. There is growing demand for other secondary materials, such as structural steel. In one demonstrator project on which this case is based, the time involved in deconstructing a steel frame was estimated to add £50/tonne – but additional resale value is currently around £80/tonne. If it’s assumed that 20% of the deconstructed steel is lost to cutting, the deconstruction option becomes 8% more expensive than typical demolition and scrappage. For brick laid in cement mortar, a demonstrator found that costs were heavily dependent on the deconstruction method. Using an excavator, despite breaking more bricks, produced reusable bricks at a cost 48% lower than other reclaimed bricks on the market, and 24% lower than virgin bricks.
Feasibility: Improving skills and technology will simplify deconstruction and reduce time and cost. Greater familiarity with markets for secondary materials will simplify identification of materials that can be resold and reduce transaction costs.
Risk: Shifting from demolition to deconstruction and urban mining minimises businesses’ exposure to the risk of demolition becoming an unacceptable approach in many contexts. Supplying materials directly to other construction projects may require the development of testing procedures and warrantying. Demolition contractors could integrate these operations or supply to specialists who prepare products for resale.
Scalability: Greater demand for secondary materials from across the market, driven by progressive purchasing and tighter regulation of whole life carbon or carbon pricing, will increase margins between deconstruction costs and resale prices. This will allow more material types to be profitably recovered.
Related demonstrators: Demonstrator 5 – Stablen / The Stack, Demonstrator 8 – Vantaankoski school, Demonstrator 9 – Tikkurila School Warehouse, Demonstrator 10 – Component reuse of retail unit.
Further reading
For further information about these outputs and the work behind them, please read the following reports, which were published by members of CIRCuIT partner organisations during the lifetime of the project.
D4.1 Documentation with audit result, inventory and demolition guide for execution
D4.2 Achieved reuse, refurbishment and recycling quota energy and resource balances and cost analyses for the demonstrator cases
D4.3 Recommendation for improving the use of recycled materials and reusable elements
All these reports can be downloaded at circuit-project.eu/post/latest-circuit-reports-and-publications
Acknowledgements
The following individuals authored the deliverables that form the basis of this chapter.
Andrea Charlson, ReLondon
Anja Giebelhausen, Hamburg University of Technology
Anne-Mette Manelius , Vandkunsten Architects
Antony Maubach-Howard, Hamburg University of Technology
Benedicte Krone, Plan 1 Cobblestone Architects
Colin Rose, ReLondon
Frederik Fenger Petersen, The City of Copenhagen
Janus zum Brock, Hamburg University of Technology
Johannes Braun, e-hoch-3
Kaie Small-Warner, The Building Research Establishment
Kerstin Kuchta, Hamburg University of Technology
Kimmo Nekkula, The City of Vantaa
Lotte Bjerregaard Jensen, Technical University of Denmark
Maike Hora, e-hoch-3
Marco Abis, Hamburg University of Technology
Mario Kolkwitz, Tampere University
Mathias Martin Kyed, Arkitema Architects
Mathias Peitersen, The City of Copenhagen
Mette Damgaard Nielsen, Plan 1 Cobblestone Architects
Miriam Akou, e-hoch-3
Morten Kjer Jeppesen
Peter Swallow, Grimshaw Architects
Rachel Singer, ReLondon
Rune Andersen, Technical University of Denmark
Salma Zavari, Vandkunsten Architects
Satu Huuhka, Tampere University
Shirin Gomez, e-hoch-3
Sofie Stilling, Vandkunsten Architects
Søren Nielse, Vandkunsten Architects
Tapio Kaasalainen, Tampere University
Tessa Devreese, ReLondon
Uta Mense, The City of Hamburg
Vanessa Jacobsen, Otto Wulff
Image credits
Frank Beister, Otto Wulff
Anders Bang Kiertzner, Lendager
Kimmo Nekkula, The City of Vantaa
Gareth Owen Lloyd, Clear Village
Tessa Devreese, ReLondon